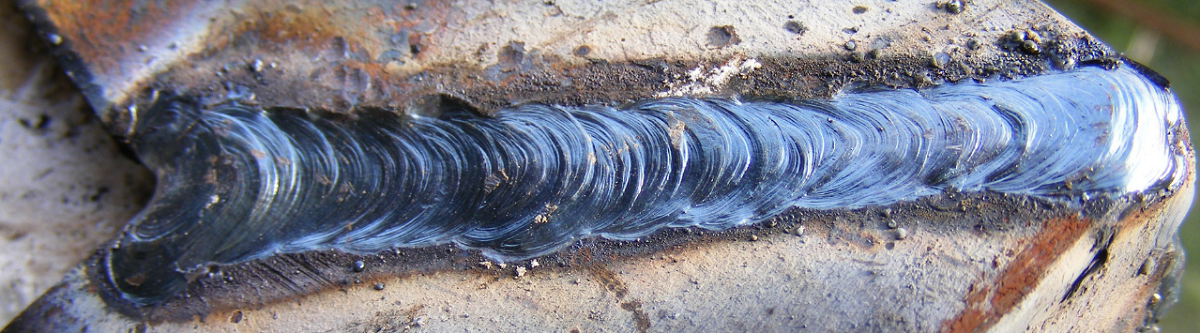
Ultra-Simple Welding Joints Guide
Welding joint is a configuration or an arrangement of the 2 pieces of metal or more that will be welded together. Pieces that are joined through welding may be in the form of a pipe, sheet, rolled plate shapes, or the portions may be forgings, billets, or castings. Welded joints should be made to ensure that the weld quality and type can be adequately accomplished under the different fabricating conditions. Joint structure is highly significant in deciding whether the welded joint can withstand the load that's imposed on it. It's a practical solution that provides superior strength for a number of different application to hold under strain and function. These welds offer low weight, high strength, rigidity, and lower cost in production.Design
Welding joints are designed to transmit the stresses between the components of the joint and throughout the weldment. Loads and forces are introduced at different points and transferred to various areas throughout the weldment. The type of service and loading of the weldment impacts significantly on the joint design.
The joint should be designed so that its cross-sectional space is the minimum possible. The cross-sectional area is a measurement of the amount or weight of weld metal that should be applied to form the joint.
Classification
All welding joints can be classified into 2 main classes: partial penetration joints and full penetration joints.- A partial penetration joint has an unfused area, and the weld doesn't completely penetrate the joint,
- A full penetration joint has weld metal throughout the entire profile of the weld joint.
Welded Joint Alloys
When welding alloy or heat-treated materials, special precautions should be taken to ensure the welding heat doesn't "break down" the heat treatment of the base metal, causing it to revert to its lower strength. Carbon and Low Alloy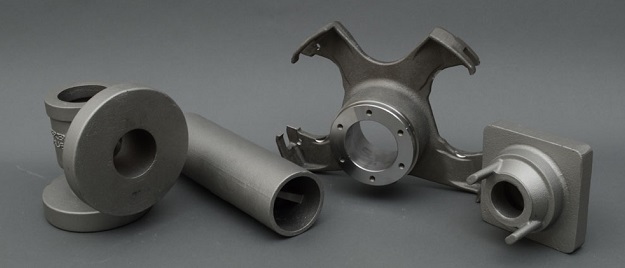
These welding joints are prepared either by machining, grinding or by flame cutting, according to the joint details. Before welding, the joint area should be cleared of all undesired materials such as dirt or paint.
Light grinding or suitable solvents can be used for cleaning. The joint surface shouldn’t be gouged or nicked since gouges and nicks may interfere with the welding operation.
Stainless Steel Alloy
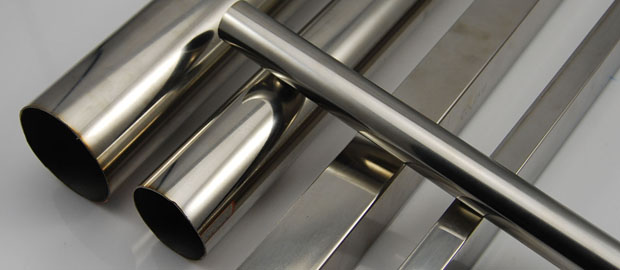
These joints are prepared by grinding, machining or by plasma arc cutting, depending on the alloy. Before welding, the joint areas should be cleaned of all unwanted material, such as paint, oxides, and dirt.
Cleaning may be done with suitable solvents like acetone or light grinding. Care should be taken to avoid gouging or nicking of the joint surface since such drawbacks can "obstruct" the welding operation.
Types of Welding Joints
The proper or improper type of joint may materially affect the strength and quality of the weld. The choosing of adequate type of weld joint depends on many factors, such as the size of the pieces being welded, desired physical properties in the finished joint, joint thickness and material, accessibility of the joint, available edge preparation equipment, fit-up obtainable, specifications of regulatory codes, and a number of pieces to be welded. 5 main types of welding joints are most commonly known and used according to AWS (American Welding Society) and many other standards. Those are T joint, lap joint, corner joint, edge joint, and butt joint.T Joint Weld
It's a joint on which the base metal is perpendicularly configured to each other, and the welding is done as fillet weld on both side or one side of the joint. T-joint and any other fillet joints aren’t commonly prepared with groove unless the base metal is thick and welding on both sides aren’t adequate to withstand the load imposed on the joint. T joint weld has its application in many components that aren’t possible to be weld except perpendicularly. It can be welded with almost all welding method while some complication occurs when fused with SAW (Submerged Arc Welding).A defect that exclusively associated with T joint is lamellar tearing. Lamellar tearing occurs because of the high constraint experienced by the joint. Still, this defect is also common in any other fillet weld joint.
Avoid joint deformation by placing stopper is a universal practice among welders. While it’s useful to minimize and prevent distortion, the material experiences a lot of stress that builds up in the weakest layer before its tears or cracks.
It’s crucial to weld the joint properly since the inadequately welding may burden the material. Different types of defects that may occur include slag inclusion, porosity, cracking, incomplete penetration, and lack of fusion. All of them can be manipulated by controlling the welding variable.
Welding Methods Used To Make T-Joints:
- Fillet weld;
- Plug weld;
- Slot weld;
- Bevel-groove weld;
- J-groove weld;
- Melt-through weld;
- Flare-bevel-groove weld.

Butt Joint
Butt joint consists of placing 2 “segments” side by side and joining to make a single piece. When piece thickness enhances, or full penetration is desired, they are beveled. These are referred to as groove welds. Beveling augments the amount of filler metal required but ensures right penetration and higher strength. Being the universally accepted method for attaching a pipe to itself, butt joint is also applied for flanges, valves, fittings, and other things. It’s the simplest and probably the most applicated type of welding joints in the construction industry.Welding Methods Used To Make Butt Joints:
- Square-groove butt weld;
- Bevel-groove weld;
- J-groove butt weld;
- V-groove butt weld;
- U-groove butt weld;
- Flare-V-groove butt weld;
- Flare-bevel-groove butt weld;

Lap Joint
It’s a modification of butt joint, where the material that’s on the same level is structured to overlay each other and then fillet welded. Anyhow, there is also another welding technique that can be applied to lap joint like spot weld, slot weld, and plug weld. The application for this joint is mostly applied on sheet metal while it’s also used on thicker material such as pipe and plates. The base metal isn’t usually grooved when fillet welded. In other welding methods such as plug and slot weld a special preparation is needed to give some type of blueprint. There’re several drawbacks in lap joint weld. For example, the lamellar tearing may also commonly occur in thicker material whether it is fillet welded or slot and plug welded. The issue of corrosion can also happen due to the wide contact surface on which the material overlaps.Welding Methods Used To Make Lap Joints:
- Plug weld;
- Slot weld;
- Spot weld;
- Bevel-groove weld;
- J-groove weld;
- Flare-bevel-groove weld.

Corner Joint
Corner joint is much alike T-joint, the difference is the location of the metal in which T joint is positioned. It's placed in the middle from the corner of the metal. However, in the corner weld, the edge of both metals meet in either open or closed style. It looks like the corner of a box where the 2 perpendicular metal meets. Therefore, the application of this joint is mostly on a metal box construction or any construction that resembles a box. Defects associated with corner joint are lamellar tearing, incomplete penetration, porosity, and slag inclusion, just like the case with T joint. To reduce the occurrence of these defects a little variation can be used. Apply alternatives such as grooving the welded metal and applying open corner joint instead of a closed corner joint.Welding Used To Make Corner Joints:
- Fillet weld;
- Spot weld;
- Square-groove weld;
- V-groove weld;
- Bevel-groove weld;
- U-groove weld;
- Corner-flange weld;
- Flare-V-groove weld;
- J-groove weld;
- Edge weld.
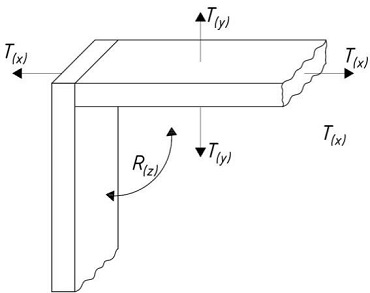
Edge Joint
Edge joint is similar to lap joint where parts of the base metal are overlapping each other, but instead of fillet welded edge, joint is butt welded on the thickness side where the end of the metal faces. Edge joint welding is also similar to flanged butt joint and flanged corner joint, where part of the base metal is welded and bent on the end side. Since there’s a contact area of the 2 metal, corrosion is an issue. It causes defects such as slag inclusion, lack of fusion, and porosity just like in any other joint.Welding Methods Used To Make Edge Joints:
- Corner-flange weld;
- U-groove weld;
- V-groove weld;
- Edge-flange weld;
- J-groove weld;
- Square-groove weld;
- Bevel-groove weld.

Benefits
Welding is a frequently used permanent joining method. Through great advancement in welding technology, welding joint has secured a notable place in fabricating all kind of applications and components. A welded joint has the following benefits:- Compared to other types of joints, the welded joint has higher efficiency;
- An efficiency of 90 % is easily possible;
- Since the amount of added material is minimum, the joint has lighter weight;
- Weld joints have sleek appearances;
- Because of flexibility during the welding process, addition and alteration are possible;
- Making a joint in difficult locations is possible with welding.