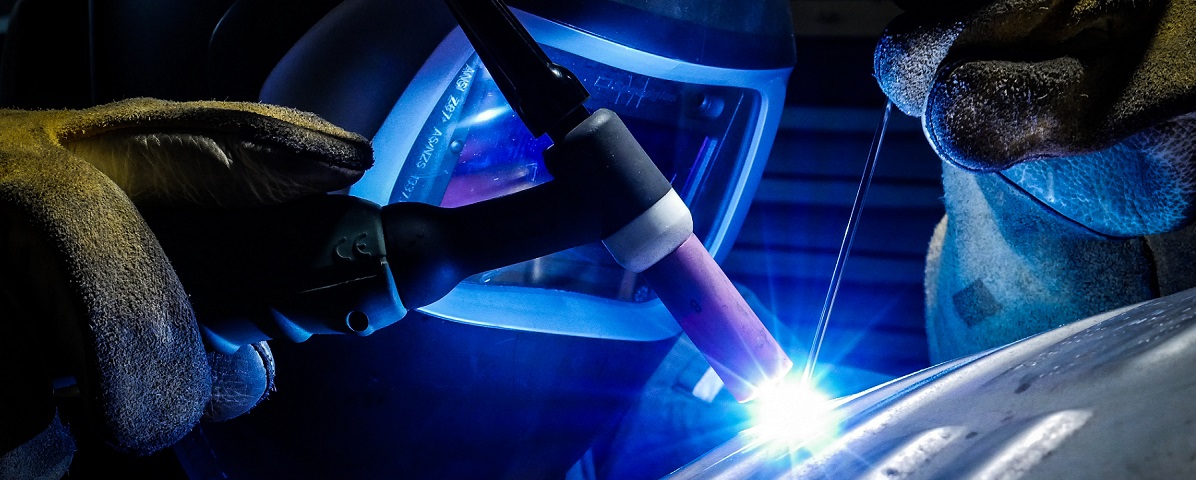
Welding – The Art of Metal Fusing from Bronze to Information Age
From iron to information age different empires were born and collapsed, various nations, animals, and crafts vanished or disappeared, but something is still here – the welding and welders of course. Do you know that, according to the American Welding Society, an estimated 50% of the United States gross national product is generated by welding? Welding is pivotal for U.S. economy. Anything made of metal, no matter how big or small, can be welded. Skyscrapers, highways, oil and natural-gas pipelines, giant wind turbines, and solar panels would be impossible to build without welding. Welding ranks high among industrial processes and spans more variables and sciences than those involved in any other industrial process.Welding Definition
Welding is the operation of joining together two chunks of metal so that bonding takes place at their original boundary surfaces. When two pieces to be fused are melted together, pressure or heat or both are used with or without added metal for formation of the metallic joint.
What is Welding?
The process of welding doesn’t only bond the two metal parts together as in soldering and brazing, but, through the use of extreme heat and sometimes the addition of other metals or gases, “forces” the metal structures of the two pieces to join together and become one. There are many various welding methods such as spot welding, metal inert gas, and tungsten inert gas, arc welding, gas welding, and underwater welding. Almost everything you use in daily life is welded or made by equipment that is fused. Welders help build metal products from coffee pots to skyscrapers. They help build space vehicles and millions of other products ranging from oil drilling rigs to automobiles. In construction, welding is practically rebuilding the world, with a project such as extending subways, building bridges, and helping in the protection of the environment by building contamination control devices. The use of welding is virtually limitless.When was Welding Invented?
As you might assume, welding has been around for quite some time now. Actually, you can suppose welding existed in some form as far back as the Bronze Age and the Iron Age. There are indicates that the Egyptians learned to weld iron together, and the evidence is founded small gold boxes with lap joints pressure welded from over 2,000 years ago. In the Middle Age development a quite simple technique of welding that typically involved only hammering two parts of metal together under heat until they join. Conventional welding as we know didn’t appear until the 19th century.History of Welding Year by Year
The “tale” begins with the discovery and shaping metals in ancient civilizations from copper to iron age. Metalworking then progressed onto steel. Many people believe welding was a process developed when the industrial revolution came about. In reality, its origins can actually be traced much further back in history. This welding history timeline below details how the technology developed over the centuries.Middle Ages During the Middle Ages, blacksmiths welded various types of iron tools by hammering. The welding techniques persisted more or less same until the beginning of the 19th century. 1800 In the 19th century, significant changes in welding happened. The use of open flame was a crucial turning point in the welding history since open flame allowed the manufacture of complex metal equipment and tools. Britishman Edmund Davy discovered acetylene in 1836, and it was soon applied by the welding industry. In 1800, Sir Humphrey Davy designed a battery-operated device which could make an arc between carbon electrodes. It was amply utilized in welding metals. 1880 In 1881, a scientist from France, Auguste De Meritens performed fusing lead plates by applying the heat derived from an arc. Later, Russian scientists Stanislaus Olszewski and Nikolai N. Benardos promoted an electrode holder for which they awarded British and US patents. 1890 In 1890, C.L. Coffin was “earned” the first U.S. patent for an arc welding process employing a metal electrode. It was the first record of the metal melted from the electrode transferred via the arc to store filler metal in the joint to create a weld. About the same time, N.G. Slavianoff, a Russian, presented the similar concept of transferring metal across an arc, but to pour out metal in a mold. 1900 A coated metal electrode was first released in 1900 by Strohmenger. A lime coating helped the arc to be much more stable. Many other welding processes were developed during this period. Some of them included spot welding, seam welding, projection welding, and flash butt welding. 1920 Soon after the World War I, twenty members of the Wartime Welding Committee of the Emergency Fleet Corporation, led by Comfort Avery Adams, established the American Welding Society as a nonprofit organization dedicated to the development of welding and associated processes. Automatic welding was first introduced in 1920. Invented by P.O. Nobel, automatic welding integrated the use of arc voltage and bare electrode wires. It was used for repairing and molding metals. Several types of electrodes were also developed during this decade.

1930 In 1930, the New York Navy Yard developed stud welding. It was mainly exploited for the construction industry and also for shipbuilding. It was during this time that the National Tube Company introduced a welding process named smothered arc welding. In the shipbuilding industry, the stud welding was substituted by the more sophisticated submerged arc welding. 1940 A new style of welding for seamlessly welding magnesium and aluminum was presented in 1941 by Meredith. This patented process was known as Heliarc welding. The GTAW or gas shielded metal arc welding was another significant discovery in the history of welding which was developed in Battelle Memorial Institute in 1948. 1950 The carbon dioxide (CO2) welding process developed by Novoshilov and Lyubavskii in 1953 became a first welding option for welding steels, as it was a budget-friendly solution. Soon, electrode wires of smaller diameter were designed. It’ll make welding of thin materials more suitable. 1960 There were several advancements in the welding industry during the 1960s. Innershield, Dualshield, and Electroslag welding were some of the significant welding advancements of the decade. Plasma arc welding was also developed by Robert Gage during this period. It was used for metal spraying. The French also launched electron beam welding, which is still utilities by the aircraft manufacturing industries in the United States. Today

Friction welding, which applies rotational speed and boosts pressure to produce friction heat, was developed in the Soviet Union. It’s a special method and has applications only where a sucient volume of similar parts is to be welded because of the high expense for tools and equipment.
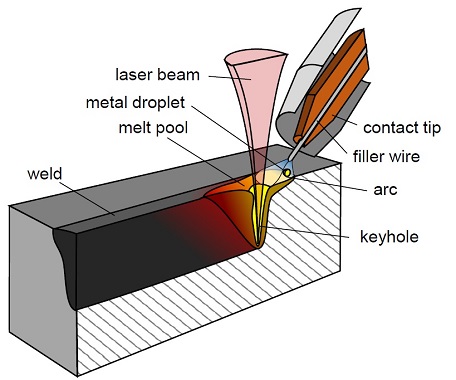
Laser welding is one of the latest methods. The laser was developed initially at the Bell Telephone Laboratories as a communications device. Because of the enormous concentration of energy in a small space, it turned out to be a great heat source. It's used for cutting metals and nonmetals.
Who Invented Welding
There is no one individual to credit with the invention of welding. Some of the earliest progress of rudimentary welding came about in 1800. In that year, Sir Humphry Davy designed the first electric arc among 2 carbon electrodes by use of a battery. In 1836, Edmund Davy found acetylene. But it wasn’t until 1881 that true welding was invented. It began with professor August De Meritens, who used arc heat to join lead plates together. His Russian student Nikolai Benardos then patented a technique of electric arc welding with carbon rods. After that, welding processes inroaded rapidly. Nikolai Slavynov realizes how to use metal electrodes for welding, and following this, C.L. Coffin, an American engineer, invented an arc welding process using a coated metal electrode that became the prototype of shielded metal arc welding.What Does a Welder Do
A welder or lit operator “sculpture” and fuses metal parts. Welders fabricate this through the use of different devices that produce intense heat. They also polish and smooth the metal surfaces once fused together. They are vital players in the manufacturing and constructing many structures, and products people rely on daily, across the country. Lit operators use various styles of welding processes to integrate the metal joints and components found in a range of industries and products. Also, welders must adhere the safety standards, perform practices to prepare equipment and materials for welding, and control and regulate welded products to ensure they’re safe to use.How to Become a Welder
Most of them have a high-school diploma and a professional certification. Certifications can be gained at community colleges, private programs, or vocational schools. OTJ (on-the-job training) is often included in these training programs. OTJ-s usually included are shop mathematics, blueprint reading, mechanical drawing, chemistry, physics, and metallurgy classes. A welder can also acquire certification through the American Welding Society.Welder Job Description
Their primary obligation is fusing metal parts together. Welders work on metal components of a variety of construction or building industries. Examples include but aren't limited to pipelines, bridges, power-plants, or refineries. They may also work in manufacturing ships or cars. Welders monitor the machinery and equipment they work with. Because of the wide variety of work and industries, they work in more than 100 different welding processes, and the most prevalent is arc welding.Work-Time of a Welder
They work full-time and often must work overtime. Welders can work up to ten hours per day if required. Lit operators typically work outdoors and are exposed to hazardous situations on a daily basis. Condition as confined spaces, on scaffolding, or inclement weather are the part of welder’s job too. These with the highest skill levels and an enthusiasm to migrate have the starting advantage for employment.Welding Methods
Nowadays many various welding methods are used. So, it’s vital to figure out first some of the standard welding techniques before making your first weld. Here is the list of basic welding methods used today:MIG
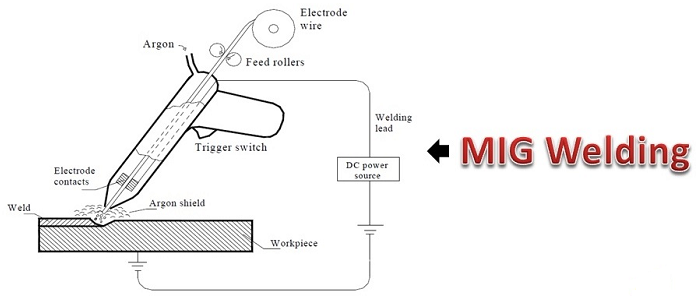
MIG means for metal inert gas welding, which is the same as GMAW (gas metal arc welding), or MAG (metal active gas welding). MIG applies a consumable electrode and an argon-carbon dioxide shielding gas to produce powerful welds on both thick and thin sheets of metal. It’s one of the most typical welding method and the easiest to learn. Therefore, it's excellent for both large-scale production and beginners.
TIG

TIG or tungsten inert gas welding, but you might also see it referred to GTAW (gas tungsten arc welding). TIG seems almost the same as MIG, except that the electrode is non-consumable and the shielding gas typically has an argon-helium composition. TIG is a more difficult process to learn than MIG since it requires a more welding skill. So, it’s typically used by more experienced welders for complex projects which demand a clean finish.
FCAW

FCAW symbolizes flux-cored arc welding. This method uses different equipment from TIG and MIG welding, while the electrode is a continuously-fed consumable such as MIG. It can fabricate hazardous gases, so it's crucial to wear proper protection like a welding helmet. Still, if adequate care is taken with safety as well as technique, then FCAW is an incredibly quick, portable process which is ideal for manufacturing.
SMAW

SMAW or suitable shielded metal arc welding, but it’s also known as stick welding. Like FCAW, it uses ux to protect the weld pool from damaging atmospheric gases. It’s a slightly easier method to learn than FCAW since it needs less equipment and less experience. It can be used with most metals like industrial steel and iron, making it one of the most popular and widely utilized welding methods ever.
GMAW
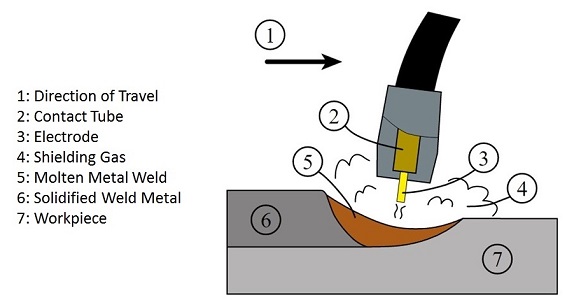
GMAW is a shortcut of gas metal arc welding, which is a welding terminology that encompasses both MAG and MIG welding. All these methods use the same technique of forming an electric arc between metal and an electrode. It heats the metal and forces it to melt while making a joint which joins the metal parts together. GMAW requires a shielding gas to guard the weld pool from atmospheric gases, so it isn't adequate for outdoor tasks. If any wind blows the gas away from the weld pool, the welder will end up with porous, defective joints. However, when used indoors GMAW is an incredibly versatile method.
Welding Essentials
Before you begin with welding, it’ll be helpful to take a class or nd an expert who can teach you how to weld. In case, you fail to master the simple safety requirements, you can seriously burn yourself or damage eyes. The process of welding fusses metal together by melting two pieces of metal at a seam and making a joint. To get started with the welding basics, you’ll need a welder, electrodes, feeds, handy tools, and safety gear.TIG and MIG Welders

The most typical welder utilized in basic projects by hobbyists and homeowners is the stick welder. Also known as the shielded metal arc welder, most folks favor it since it’s quite easy to purchase, and there is no need for a special environment to use it.
However, the electrodes in a stick welder require much replacement compared with other kinds of welding. These include gas metal arc welder and the gas tungsten arc machines. You’ll need some type of gas feed with this kind of welder, too.